
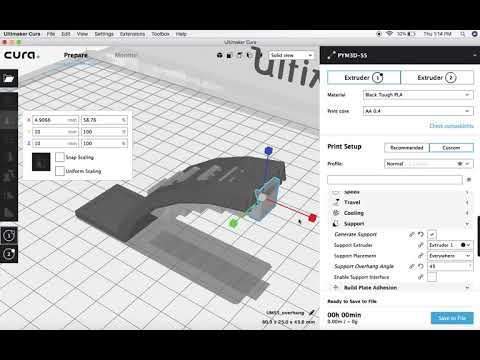
The approach taken for these materials is to produce the intended part using support structures printed in the primary build material. For example, Polycarbonate (PC), TPU 95A, Propylene (PP) each suffer from incompatibility. There are certain material bonding limitations when working with higher temperature materials. These two highly popular support materials are not without their limits. It is a better choice of support material when printing with high temperature engineering materials such as ABS, CPE+. Breakaway, as it says in the name supports can easily be pulled off, it is a very time efficient material. With PVA it is possible to print very intricate and small features and then easily dissolve the support material to be left with an exceptionally clean finish. It is important to note that when using PVA support material to keep it out of moist environments. PVA is compatible with PLA, tough PLA, CPE and Nylon. There are a number of patterns that are not only great for finding the right way to support tricky parts geometries but also solutions such as giro infill that offers more surface exposure during dissolving. If in custom mode Ultimaker Cura has even more to offer. Using Ultimaker Cura with the easy print and intent based profiles makes activating support is very easy. Breakaway material is ideal for fast removal when support features are on the outside but can be extremely difficult when extracting from internal cavities and highly complex organic surfaces. However, it is not compatible with high temperature engineering materials or materials that simply won't bond. PVA is easy to use and remove with many of Ultimaker's lower temperature materials. removing support takes post-processing time.What to remember when using support materials The benefits are, design freedom with complex geometries, overhang angles that can be less that 45 degrees, ability to produce internal cavities and single-part hinges where removing the primary build support would have been impossible.
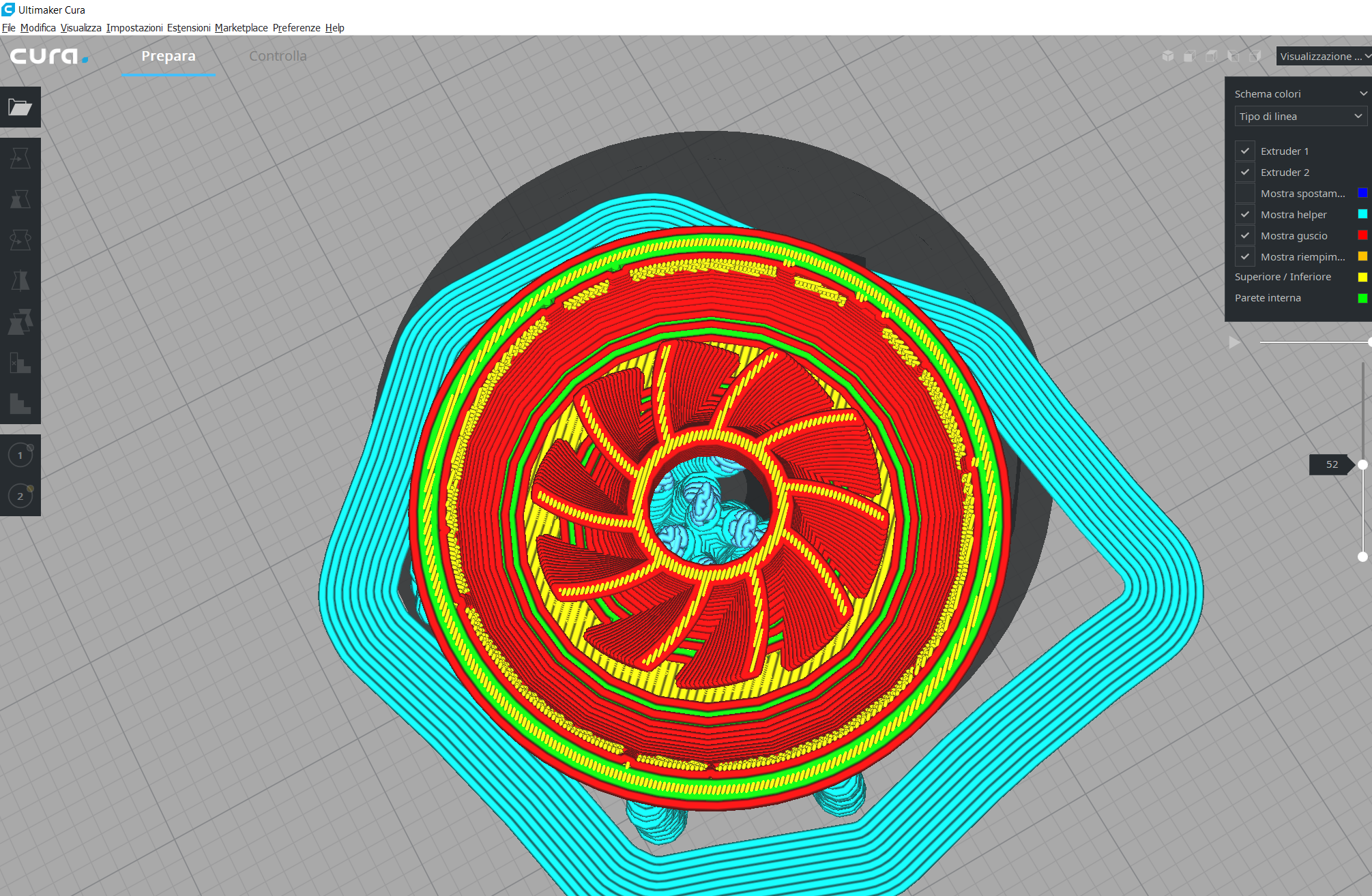
To summaries why dedicated support materials should be used. In this case PVA and other water-soluble materials which is easy to use and easy to remove can save the day. Alternatively, a part printed such as an anatomical heart has many intricate cavities these elements would be impossible to remove by hand using simple single material strategies. Architects designing model housing with supports on the outer perimeter of the object can use breakaway materials that do not chemically bond with the primary build material and can easily be pulled away from the surface using pliers. You can also match the material selected for the primary build with exactly the right support material designed to reach the intended part faster. It is now not only possible to choose a solution that perfectly matches the supports.

These materials are engineered to be easily removed from the primary build part without chipping, sanding and healing that was more typical when support scaffolds were printed using the primary build material.Īdditional strategies are possible in Ultimaker Cura for single build support techniques that gain further value in a dual extrusion machine. This opens up opportunities to print using dedicated support materials that are ideally suited to print support scaffolding. Starting with the Ultimaker 3 and following into the Ultimaker S-Line, the operator has the opportunity to build their parts with two materials at the same time. Everything from using per object settings, placing custom designed support objects to experimental techniques such as tree support patterns. Ultimaker Cura has a number of options for support materials to be generated.
ULTIMAKER CURA TREE SUPPORT SOFTWARE
Using software such as Ultimaker Cura, support material generation should be activated indicating the angle at about 45-50 degrees. The solution is to use the primary build material for the print structures. This can lead to print inaccuracies or complete print failure. It is well known that any unsupported features such as arms or overhangs would simply drip plastic onto the plate if there is nothing below to support until the print has cooled (known as dropping loops). The need for a support strategy is a standard requirement when using an additive manufacturing technology, such as FFF extrusion. Basic Support Material Strategies for FFF 3D printing
